Композиционных материалов свойства и противопоказания
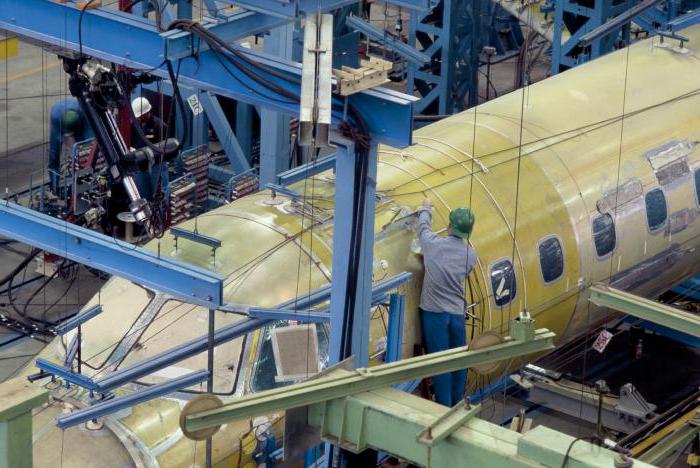
Что такое композиционный материал (композит)
Композитные материалы (КМ) – говорят, первые упоминания о подобных материалах можно найти в Библии. Композит — это материал, состоящий из двух и более компонентов, которые усиливают и дополняют свойства друг друга. Благодаря чему, конечный материал обладает свойствами, достижение которых невозможно каждым компонентом по отдельности. Возьмем, к примеру, стеклопластик. Так, если бы какая то деталь была полностью из стекла, она обладала бы очень большой теоретической прочностью на растяжение или сжатие. Но на практике, многочисленные поверхностные трещины приводят к разрушению изделия задолго до достижения ее теоретической прочности. В таком же изделии из стеклопластика, рост какой-то конкретной микротрещины ограничится обрывом одного волокна. А полимерная матрица перераспределит нагрузку на оставшиеся волокна. Примерно так работает самая обычная стеклопластиковая арматура. Так же, при изготовлении изделия можно заложить направление волокон с учетом предполагаемых направлений нагрузки на изделие. Что позволит избежать излишнего количества материалов в «ненужных» нам направлениях.
Рынок композитов в России
Доля России в мировом производстве композитов минимальна. Емкость рынка композиционных материалов, делает производство КМ одним из наиболее перспективных направлений деятельности в нашей стране. Если в 1970-е мы были 4-е в мире по производству композитов, то сейчас не обеспечиваем и 3% мирового спроса. Это в немалой степени обусловлено отсутствием своего сырья, до недавнего времени на долю импорта приходилось 90%. Но программа импорта замещения работает и в композитной отрасли, так в 2015г. на территории Татарстана было открытие завода по производству углеродного волокна. Предприятие, при выходе на полную мощность, способно полностью удовлетворить потребности российского рынка.
Так же, производство КМ в промышленном масштабе тормозит отсутствие единых технических регламентов в этой сфере. Главгосэкспертиза попросту не пропускает многие проекты в строительстве из-за отсутствия СНИПов на технологию. Тем не менее, с помощью КМ в России усилено больше тысячи строительных объектов. Так в 2014г . в Башкирии 5 мостов были усилены лентами (в основе которых углеродное волокно и эпоксидная смола) для провоза по ним крупногабаритного оборудования ОАО «Газпром» весом почти 100т.
Применение композитных материалов в технике
Полимерные КМ имеют неоспоримый ряд преимуществ в сравнении с металлоконструкциями. Таких как: эксплуатационно-технические, -экономические, технологические. Именно поэтому они (в основном углепластик и стеклопластик) получили широкое применение почти во всех отраслях промышленности.
Авиация
В самолетостроении композитные материалы начали применять еще с 1940-ых, в настоящее же время доля КМ в некоторых образцах достигает 50% (Boeing787 Dreamliner). Из КМ изготавливаются такие детали как: обшивка, руль высоты, руль направления, обтекатели, воздухозаборники, закрылки и т.п. К примеру: замена элементов крепления лопастей к ротору на стеклопластиковые, в некоторых моделях вертолетов, позволила снизить массу деталей на 40%, а стоимость в 2,5 раза.
Ракетная техника
Одними из первых стеклопластиковых деталей, примененных в 60-х годах, в ракетной технике, стали корпуса двигателей боевых ракет. Дальность таких ракет увеличилась с 1500 до 4000км. Сейчас, доля КМ в некоторых типах ракет доходит до 85-90% от общей массы.
Космические аппараты
Посчитано что экономическая выгода от снижения массы космического аппарата всего на 1кг составляет от10000 $ до 50 000 $. Наилучших показателей в снижении веса космических аппаратов удалось добиться только с применением КМ. К концу прошлого века доля композитов в конструкции составляла 20%.
Автомобилестроение
Применение композитов в машиностроении так же продолжает набирать обороты. Сейчас есть проекты создания автомобилей с максимальным применением КМ. Расход топлива такого автомобиля должен составить менее 2,5л на 100км.
Углепластик, стеклопластик, кевларопластик в основе которых эпоксидная и полиэфирная смола и многие другие виды КМ так же обширно применяются в судостроении, железнодорожном транспорте, спортивной технике, строительстве. В качестве только развивающихся видов техники можно выделить радиотехнику, военную технику, ортопедические протезы и современную бытовую технику.
Композитный материал-технологии изготовления
На конечные свойства изделия также влияет то, каким способом оно произведено. Некоторые методы позволяют организовать производство композитов даже у себя в гараже. И так, рассмотрим наиболее часто встречающиеся методы производства КМ:
Напыление
Рубленное волокно, перемешанное с катализированной смолой напыляется с помощью пистолета на оснастку.
Связующее : преимущественно, полиэфирная смола
Наполнитель: стекловолокно
Ручная формовка
Сухие армирующие волокна в виде полотен укладываются на матрицу, после чего наносится смола.
Вакуумное формование
После укладки и пропитки ткани как при ручной формовке, на стадии отверждения, применяется давление для укрепления ламината.
Связующее : чаще, эпоксидная смола или фенольная
Намотка
Волокна, пропитанные связующим, наматываются в различных направлениях на оправку. Пример: стеклопластиковые трубы или баллоны.
Пултрузия
Процесс производства профильных изделий из одноосно-ориентированных пластиков непрерывным способом, является аналогией экструзии металлов.
RTM
Сухой армирующий слой укладывается на оснастку, затем вторая часть оснастки закрывается и происходит инъекция смолы в полость.
Автоклав
Препрег (предварительно пропитанное волокно или ткань) выкладывается на поверхность оснастки. Затем оснастка нагревается под давлением до 120-180 °С. Давление создается автоклавом, а высокая температура активирует катализатор в связующем.
Связующее: обычно эпоксидная, полиэфирная или фенольная смола
Наполнитель: чаще всего углеродное или стекловолкно.
В заключение
ХХI век давно называют веком композитных материалов, как были каменные и бронзовые века в древности. Композиты прочно вошли в нашу жизнь, изделия из углепластика и стеклопластика можно встретить во всех отраслях промышленности и в быту. Ясно, что у российского рынка композитов колоссальный потенциал. Производству ПКМ способствуют различные Государственные программы. Технология изготовления изделий из композиционных материалов вошла в число 27 приоритетных направлений, предусмотренных Указом №899 «Об утверждении приоритетных направлений развития науки, технологий и техники в РФ и перечня критических технологий РФ». Владение базовой теорией композитов может пригодиться и в быту от ремонта стеклопластиковой душевой кабины до упрочнения фундамента домов углеродной лентой. О перспективах компаний производящих композитные материалы не приходиться и говорить.
Буду признателен за любую обратную связь. Спасибо!
Источник
1.Физико-химические свойства композиционных материалов, показания к применению.
Свойства композиционных материалов
химического отверждения.
Положительные свойств:
– равномерная полимеризация,
– простота применения,
– минимальное время изготовления
реставрации( т.к. вноситься 1 порцией)
Отрицательные свойства.
– потемнение пломбы,
– не высокие эстетические свойства,
– низкая износостойкость,
– пористость материала и токсичность.
Свойства светоотверждаемых
композитов.
Свойства зависят от размера введенных
в состав микронаполненного композита
частиц – большого размера – 8-12 мкм
(макрогибридные композиты), малого
размера – 1-5 мкм (микрогибридные композиты),
одновременно большого и малого размера
(тотально выполненные композиты),
сверхмалого размера – до 0,0004 мкм
(наногибридные) . Введение в материал с
хорошими эстетическими свойствами
частиц большого и малого размера повышает
его механическую прочность, абразивную
износостойкость, приближает его КТР к
значениям коэффициента термического
расширения твердых тканей зубов. Введение
частиц сверхмалого размера улучшает
эстетические качества материала (в том
числе – его прозрачность) при сохранении
хороших прочностных характеристик.
Размер частиц наполнителя композиционного
материала определяет его прочностные,
эстетические (полируемость, степень
рассеивания света) свойства.
Наномеры – неассоциированные частицы
размером 20- 75 нм (0,020-0,075 мкм).
Нанокластеры – агломераты наноразмерных
частиц.
Свойства макронаполненных композиционных
материалов до 30 мкм.
Положительные свойства:
– достаточная прочность;
– рентген контрастность;
– удовлетворительные оптические
свойства.
Отрицательные свойства:
– плохая цветостойкость;
– высокая шероховатость поверхности
из-за плохой полируемости и, как результат,
вероятность быстрого накопления зубного
налета;
– высокая абразивная износостойкость.
Показания к применению:
– пломбирование полостей I, II классов
на участках, где нет высоких эстетических
требований;
– моделирования культи зуба под коронку.
Свойства микронаполненных композиционных
материалов 0,01 – 0,4 мкм
Положительные свойства:
– хорошая полируемость;
– хорошие эстетические свойства;
– низкая абразивная износостойкость.
Отрицательные свойства:
– недостаточная механическая прочность;
– высокий коэффициент термического
расширения.
Показания к применению:
– высокие эcтетические требования при
пломбировании кариозных полостей III-V
классов;
– высокие эcтетические требования при
лечении некариозных поражений (клиновидных
дефектов, эрозии эмали, гипоплазии и
др.).
Свойства гибридных композиционных
материалов.
Эти материалы сочетают положительные
и отрицательные свойства макро- и
микронаполненных композиционных
материалов. Свойства зависят от размера
введенных в состав микронаполненного
композита частиц – большого размера– 8-12 мкм (макрогибридные композиты),малого размера– 1-5 мкм (микрогибридные
композиты), одновременно большого и
малого размера (тотально выполненные
композиты),сверхмалого размера–
до 0,0004 мкм (наногибридные) . Введение в
материал с хорошими эстетическими
свойствами частиц большого и малого
размера повышает его механическую
прочность, абразивную износостойкость,
приближает его КТР к значениям коэффициента
термического расширения твердых тканей
зубов. Введение частиц сверхмалого
размера улучшает эстетические качества
материала (в том числе – его прозрачность)
при сохранении хороших прочностных
характеристик.
Размер частиц наполнителя композиционного
материала определяет его прочностные,
эстетические (полируемость, степень
рассеивания света) свойства.
Наномеры – неассоциированные частицы
размером 20- 75 нм (0,020-0,075 мкм).
Нанокластеры – агломераты наноразмерных
частиц.
Показания к применению
Гибридные композиты считаются
универсальными пломбировочными
материалами, но в ряде случаев реставрации
полостей II, IV, V классов не всегда
эффективны в связи с недостаточно
идеальной поверхностью композиционной
пломбы (за исключением наногибридных
композитов).
Свойства микрогибридных композиционных
материалов
Обладают хорошими физико-химическими
качествами, они устойчивы к отлому,
имеют низкое водопоглощение, КТР
приближен к КТР твердых тканей зуба,
обладают высокой сопротивляемостью
при изгибе и сдавливании, рентгеноконтрастны.
Положительные свойства:
– высокие эстетические свойства;
– хорошая полируемость;
– цветостабильность реставраций;
– большая шкала оттенков;
– простая методика применения.
Показания к применению:
– эстетические реставрации всех полостей
по Блэку;
– изготовление виниров;
– починка сколов металлокерамики и
керамики;
– техника “ламинирования” (микрогибрид
– микрофил).
Показания к применению композиционных
материалов следующие:
– реставрация кариозных поражений,
включая все полости по Блэку;
– некариозные поражения;
– аномалии формы и цвета зубов;
– травмы зубов;
– изменения зубов по цвету;
– коррекция формы зубов;
– герметизация фиссур.
Общие противопоказания к использованию
композиционных материалов:
– неудовлетворительная гигиена полости
рта;
– бруксизм;
– патологический прикус;
– повышенная стираемость твердых тканей
зубов;
– патология тканей пародонта;
– поддесневая полость;
– профессиональные вредности.
Относительные противопоказания к
применению композиционных материалов:
– кариозная полость более 1/2объема
твердых тканей коронки зуба;
– кариозная полость “уходит” под
десну;
– металлическая коронка зуба-антагониста;
– отсутствие зубов в боковых отделах.
Соседние файлы в предмете [НЕСОРТИРОВАННОЕ]
- #
- #
- #
- #
- #
- #
- #
- #
- #
- #
- #
Источник
Виды и свойства композиционных материалов
Композиционные материалы (композиты) состоят из двух или более компонентов, причем каждый из компонентов сохраняет свои свойства (рис. 31). Один из компонентов композита является матрицей. Она располагается непрерывно по всему объему материала и является связующим материалом. Второй компонент, разделяющийся в объеме композиции, называется армирующим (наполнителем). Наполнитель усиливает композит.
Материалы матрицы и наполнителя не должны вступать в химическую реакцию друг с другом, образовывать твердых растворов, должны обладать примерно одинаковыми коэффициентами линейного и теплового расширения. В качестве материала матрицы используются металлы, полимеры, керамика и другие вещества. Армирующие компоненты — это порошковые или волокнистые материалы различной природы.
Композиционные материалы сочетают высокую удельную прочность с высокой жесткостью, обладают пониженной склонностью к трещинообразованию и высокой жаропрочностью.
Рис. 31. Схема композиционного материала:
1 — матрица; 2 — армирующие элементы; 3 — зона раздела фаз
По виду армирующего материала композиты делятся на две основные группы — дисперсно-упрочненные и волокнистые.
Дисперсно-упрочненные композиты (КМД) представляют собой металлическую матрицу, в которой равномерно распределены мелкодисперсные частицы наполнителя. Матрица является основным материалом, несущим нагрузку. Их получают с помощью порошковой металлургии. Сначала получают порошковые смеси матрицы и наполнителя, затем смеси прессуют с последующим спеканием и пластической деформацией полученной массы. Пластическая деформация повышает плотность и уменьшает пористость композита.
Широко применяются композиты с алюминиевой, магниевой, никелевой и другими матрицами. КМД на основе алюминия — САП (спеченный алюминиевый порошок). В САП матрицей является алюминий, наполнителем — мелкие частицы оксида алюминия А1203(от 6 до 18 %). С увеличением содержания оксидов алюминия повышается прочность на растяжение и уменьшается относительное удлинение. КМД на основе магния обладают низкой плотностью, высокой длительной прочностью, высоким сопротивлением ползучести. В качестве жаропрочных материалов применяют КМД с матрицей на основе никеля.
Волокнистые композиты имеют матрицу (чаще всего пластичную), армированную высокопрочными волокнами — проволокой, нитевидными кристаллами и т.д. Волокна воспринимают нагрузку и упрочняют композит. В результате совмещения наполнителя и матрицы композит приобретает свойства, которыми не обладают его компоненты. Это делает возможным создание материалов с требуемыми свойствами для определенных условий эксплуатации. Матрица должна обеспечивать монолитность композиции, фиксировать форму изделия и взаимное расположение волокон наполнителя. В зависимости от материала матрицы композиты делятся на пластики (полимерная матрица), металлокомпозиты (металлическая матрица), композиты с керамической матрицей и матрицей из углерода. Армирующие волокна должны обладать высокими жесткостью и прочностью, поэтому при создании композитов используются высокопрочные волокна из стекла, бора, углерода, металлической проволоки и нитевидных кристаллов оксидов, нитридов и других химических соединений.
Армирующие компоненты применяются в виде моноволокон, проволок, жгутов, сеток, тканей, лент, холстов.
Основное применение получили стеклянные, органические, углеродные, металлические волокна и проволоки. Тканые армирующие материалы используют для получения слоистых композитов.
Волокнистые композиты изготавливают пропиткой волокон матричным материалом. Пропитка может осуществляться расплавом при нормальном давлении, вакуумным всасыванием, под давлением и комбинированным методом.
Композиционные материалы используются на железнодорожном транспорте для изготовления композиционных тормозных колодок из асбестовой композиции шифра ТИИР-300 (8-1-66). Композиционные тормозные колодки надежны в эксплуатации, долговечны и износостойки. Они применяются на всех грузовых, а также на пассажирских вагонах, которые эксплуатируются при скоростях движения более 120 км/ч. Их изготовляют из асбокаучуковых материалов с добавлением борида, сажи и вулканизирующего состава методом напрессовки на металлический каркас. Основным недостатком таких колодок является плохой отвод тепла от поверхности вагонного колеса в процессе торможения, что может привести к образованию на поверхности катания навара, микротрещин и других повреждений.
Источник
В различных сферах промышленности используются композитные материалы. Что это такое? Это материалы на основе нескольких компонентов, что обусловливает их эксплуатационные и технологичные характеристики. В основе композитов лежит матрица на основе металла, полимера или керамики. Дополнительное армирование выполняется наполнителями в виде волокон, нитевидных кристаллов и различных частиц.
За композитами – будущее?
Пластичность, прочность, широкая сфера применения – вот чем отличаются современные композитные материалы. Что это такое с точки зрения производства? Эти материалы состоят из металлической или неметаллической основы. Для усиления материала используются нити, волокна, хлопья большей прочности. Среди композиционных материалов можно выделить пластик, который армируется борными, углеродными, стеклянными волокнами, или алюминий, армированный стальными или бериллиевыми нитями. Если комбинировать содержание компонентов, можно получать композиты разной прочности, упругости, стойкости к абразивам.
Основные типы
Классификация композитов основана на их матрице, которая может быть металлической и неметаллической. Материалы с металлической матрицей на основе алюминия, магния, никеля и их сплавов обретают дополнительную прочность за счет волокнистых материалов или тугоплавких частиц, которые не растворяются в основном металле.
Композиты с неметаллической матрицей в основе имеют полимеры, углерод или керамику. Среди полимерных матриц наиболее популярны эпоксидная, полиамидная и фенолформальдегидная. Форма композиции придается за счет матрицы, которая выступает своеобразным связующим веществом. Для упрочнения материалов используются волокна, жгуты, нити, многослойные ткани.
Изготовление композитных материалов ведется на основе следующих технологических методов:
- пропитка армирующих волокон матричным материалом;
- формование в пресс-форме лент упрочнителя и матрицы;
- холодное прессование компонентов с дальнейшим спеканием;
- электрохимическое нанесение покрытия на волокна и дальнейшее прессование;
- осаждение матрицы плазменным напылением и последующее обжатие.
Какой упрочнитель?
Во многих сферах промышленности нашли применение композитные материалы. Что это такое, мы уже сказали. Это материалы на основе нескольких компонентов, которые обязательно упрочняются специальными волокнами или кристаллами. От прочности и упругости волокон зависит и прочность самих композитов. В зависимости от вида упрочнителя все композиты можно поделить:
- на стекловолокниты;
- карбоволокниты с углеродными волокнами;
- бороволокниты;
- органоволокниты.
Упрочнительные материалы могут укладываться в две, три, четыре и больше нити, чем их больше, тем прочнее и надежнее в эксплуатации будут композиционные материалы.
Древесные композиты
Отдельно стоит упомянуть древесный композит. Он получается посредством сочетания сырья разного типа, при этом в качестве основного компонента выступает древесина. Каждый древесно-полимерный композит состоит из трех элементов:
- частиц измельченной древесины;
- термопластичного полимера (ПВХ, полиэтилена, полипропилена);
- комплекса химических добавок в виде модификаторов – их в составе материала до 5 %.
Самый популярный вид древесных композитов – это композитная доска. Ее уникальность в том, что она объединяет в себе свойства и древесины, и полимеров, что существенно расширяет сферу ее применения. Так, доска отличается плотностью (на ее показатель влияет базовая смола и плотность древесинных частичек), хорошим сопротивлением на изгиб. При этом материал экологичный, сохраняет текстуру, цвет и аромат натурального дерева. Использование композитных досок абсолютно безопасно. За счет полимерных добавок композитная доска обретает высокий уровень износостойкости и влагостойкости. Ее можно использовать для отделки террас, садовых дорожек, даже если на них приходится большая нагрузка.
Особенности производства
Древесные композиты имеют особенную структуру за счет сочетания в них полимерной основы с древесиной. Среди материалов подобного типа можно отметить древесно-стружечные, древесноволокнистые плиты разной плотности, плиты из ориентированной щепы и древесно-полимерный композит. Производство композитных материалов данного типа ведется в несколько этапов:
- Измельчается древесина. Для этого используются дробилки. После дробления древесину просеивают и делят на фракции. Если влажность сырья – выше 15 %, его обязательно высушивают.
- Дозируются и смешиваются основные компоненты в определенных пропорциях.
- Готовое изделие прессуется и форматируется для обретения товарного вида.
Основные характеристики
Мы описали самые популярные полимерные композитные материалы. Что это такое, теперь понятно. Благодаря слоистой структуре есть возможность армирования каждого слоя параллельными непрерывными волокнами. Стоит отдельно сказать о характеристиках современных композитов, которые отличаются:
- высоким значением временного сопротивления и предела выносливости;
- высоким уровнем упругости;
- прочностью, которая достигается армированием слоев;
- за счет жестких армирующих волокон композиты обладают высокой стойкостью к напряжениям на разрыв.
Композиты на основе металлов отличаются высокой прочностью и жаропрочностью, при этом они практически неэластичны. За счет структуры волокон уменьшается скорость распространения трещин, которые иногда появляются в матрице.
Полимерные материалы
Полимерные композиты представлены в многообразии вариантов, что открывает большие возможности по их использованию в разных сферах, начиная от стоматологии и заканчивая производством авиационной техники. Наполнение композитов на основе полимеров выполняется разными веществами.
Наиболее перспективными сферами использования можно считать строительство, нефтегазовую промышленность, производство автомобильного и железнодорожного транспорта. Именно на долю этих производств приходится порядка 60 % объема использования полимерных композиционных материалов.
Благодаря высокой устойчивости полимерных композитов к коррозии, ровной и плотной поверхности изделий, которые получаются методом формования, повышается надежность и долговечность эксплуатации конечного продукта.
Рассмотрим популярные виды полимерных материалов.
Стеклопластики
Для армирования этих композиционных материалов используются стеклянные волокна, сформованные из расплавленного неорганического стекла. Матрица основывается на термоактивных синтетических смолах и термопластичных полимерах, которые отличают высокая прочность, низкая теплопроводность, высокие электроизоляционные свойства. Изначально они использовались при производстве антенных обтекателей в виде куполообразных конструкций. В современном мире стеклопластики широко применяются в строительной сфере, судостроении, производстве бытового инвентаря и спортивных предметов, радиоэлектронике.
В большинстве случаев стеклопластики производятся на основе напыления. Особенно эффективен этот метод при мелко- и среднесерийном производстве, например корпусов катеров, лодок, кабин для автомобильного транспорта, железнодорожных вагонов. Технология напыления удобна экономичностью, так как не требуется раскраиваться стекломатериал.
Углепластики
Свойства композитных материалов на основе полимеров дают возможность использовать их в самых разных сферах. В них в качестве наполнителя используются углеродные волокна, получаемые из синтетических и природных волокон на основе целлюлозы, пеков. Волокно обрабатывается термически в несколько этапов. По сравнению со стеклопластиками углепластики отличаются более низкой плотностью и более высоким модулем упругости при легкости и прочности материала. Благодаря уникальным эксплуатационным свойствам углепластики находят применение в машино- и ракетостроении, производстве космической и медицинской техники, велосипедов и спортивных принадлежностей.
Боропластики
Это многокомпонентные материалы, в основе которых лежат борные волокна, введенные в термореактивную полимерную матрицу. Сами волокна представлены мононитями, жгутами, которые оплетаются вспомогательной стеклянной нитью. Большая твердость нитей обеспечивает прочность и стойкость материала к агрессивным факторам, но при этом боропластики отличаются хрупкостью, что осложняет обработку. Борные волокна стоят дорого, поэтому сфера применения боропластиков ограничена в основном авиационной и космической промышленностью.
Органопластики
В этих композитах в качестве наполнителей выступают в основном синтетические волокна – жгуты, нити, ткани, бумага. Среди особенных свойств этих полимеров можно отметить низкую плотность, легкость по сравнению со стекло- и углепластиками, высокую прочность при растяжении и высокое сопротивление ударам и динамическим нагрузкам. Этот композиционный материал широко используется в таких сферах, как машино-, судо-, автостроение, при производстве космической техники, химическом машиностроении.
В чем эффективность?
Композитные материалы за счет уникального состава могут использоваться в самых разных сферах:
- в авиации при производстве деталей самолетов и двигателей;
- космической технике для производства силовых конструкций аппаратов, которые подвергаются нагреванию;
- автомобилестроении для создания облегченных кузовов, рам, панелей, бамперов;
- горной промышленности при производстве бурового инструмента;
- гражданском строительстве для создания пролетов мостов, элементов сборных конструкций на высотных сооружениях.
Использование композитов позволяет увеличить мощность двигателей, энергетических установок, уменьшая при этом массу машин и оборудования.
Какие перспективы?
По мнению представителей сферы промышленности России, композиционный материал относится к материалам нового поколения. Планируется, что к 2020 году вырастут объемы внутреннего производства продукции композитной отрасли. Уже сейчас на территории страны реализуются пилотные проекты, направленные на разработку композитных материалов нового поколения.
Применение композитов целесообразно в самых разных сферах, но наиболее эффективно оно в отраслях, связанных с высокими технологиями. Например, сегодня ни один летательный аппарат не создается без использования композитов, а в некоторых из них используется порядка 60 % полимерных композитов.
Благодаря возможности совмещения различных армирующих элементов и матриц можно получить композицию с определенным набором характеристик. А это, в свою очередь, дает возможность применять эти материалы в самых разных сферах.
Источник